Preventing Frost Heave in Cold Regions: The Role of Trace Heating Cables and Material Considerations
Abstract
Frost heave, the upward movement of soil due to ice lens formation, poses a significant threat to infrastructure in cold regions. This article investigates the role of trace heating cables in mitigating frost heave, focusing on the critical aspect of material considerations for optimal performance and longevity. Key findings highlight the effectiveness of trace heating in preventing ice lens formation, the importance of sheath, conductor, and insulation materials, and the need for careful selection based on specific application requirements. Furthermore, the article explores the environmental impact of trace heating systems, discusses energy efficiency considerations, and examines emerging trends in trace heating technology, including case studies, life-cycle assessments, and economic analyses.
Introduction
Frost heave, a geological phenomenon characterized by the upward displacement of soil due to the expansion of freezing water, poses a significant threat to infrastructure in cold climates. Roads buckle, pipelines rupture, and building foundations crack, resulting in substantial economic losses, disruptions to essential services, and safety hazards.
This article delves into the intricacies of frost heave, exploring the underlying principles of trace heating technology as a proven mitigation strategy. We will critically examine the crucial role of material selection in ensuring the effectiveness and longevity of trace heating systems. Furthermore, we will explore the environmental impact, energy efficiency considerations, and emerging trends in trace heating technology, including real-world case studies, life-cycle assessments, and economic analyses.
Understanding Frost Heave
Frost heave is a natural process that occurs in cold climates when water in the soil freezes and expands, pushing the ground upward. This happens because water turns into ice, increasing in volume by about 9%, which creates pressure within the soil. The freezing process also draws more water from surrounding areas, forming layers of ice called ice lenses. As these ice layers grow, they force the soil to rise, leading to cracks and damage in roads, pipelines, and building foundations. When temperatures warm up, the ice melts, and the ground can sink back unevenly, causing further structural problems. Frost heave is especially common in fine-grained soils like clay and silt, which hold a lot of moisture.
Factors Influencing Frost Heave
Soil Type: Fine-grained soils, such as clay and silt, with their high water-holding capacity, are particularly susceptible to frost heave.
Water Content: The presence of sufficient moisture within the soil is a prerequisite for frost heave to occur.
Climate: Regions with prolonged periods of freezing temperatures and fluctuating temperature cycles are more prone to frost heave.
Figure 1: A schematic diagram illustrating the process of ice lens formation and soil movement during frost heave
The diagram depicts the intricate interplay between water, soil particles, and temperature fluctuations. As water within the soil freezes, it expands, exerting pressure on surrounding soil particles and pushing them upwards. The formation of ice lenses, thin layers of ice within the soil profile, further amplifies this upward movement, leading to significant ground deformation.
The Problems Frost Heave Causes for Heating Cables
Frost heave, the upward expansion of soil due to freezing, poses significant threats to underground heating cables. Here are the conventional problems that arise:
Mechanical Stress: The powerful force of expanding soil can physically damage heating cables. The constant pressure, bending, and stretching can lead to cracks in the cable's protective layers or even complete breakage of the internal wires.
Heat Loss: When the cable's insulation is compromised due to frost heave damage, heat distribution becomes uneven. This reduces the system's efficiency, leading to wasted energy and ineffective heating.
Increased Maintenance Costs: The damage caused by frost heave necessitates frequent inspections and repairs. This translates to higher operational expenses due to labor, replacement parts, and system downtime.
Uneven Thawing and Cracking: Even if the cable isn't completely broken, uneven heating can cause the ground to thaw unevenly. This can result in cracks and damage to the surface above the cables, such as driveways or patios.
Shortened Lifespan: The combined effects of physical damage, inefficient heating, and increased maintenance contribute to a shorter lifespan for the heating system. Instead of lasting for many years, a system affected by frost heave might require premature replacement.
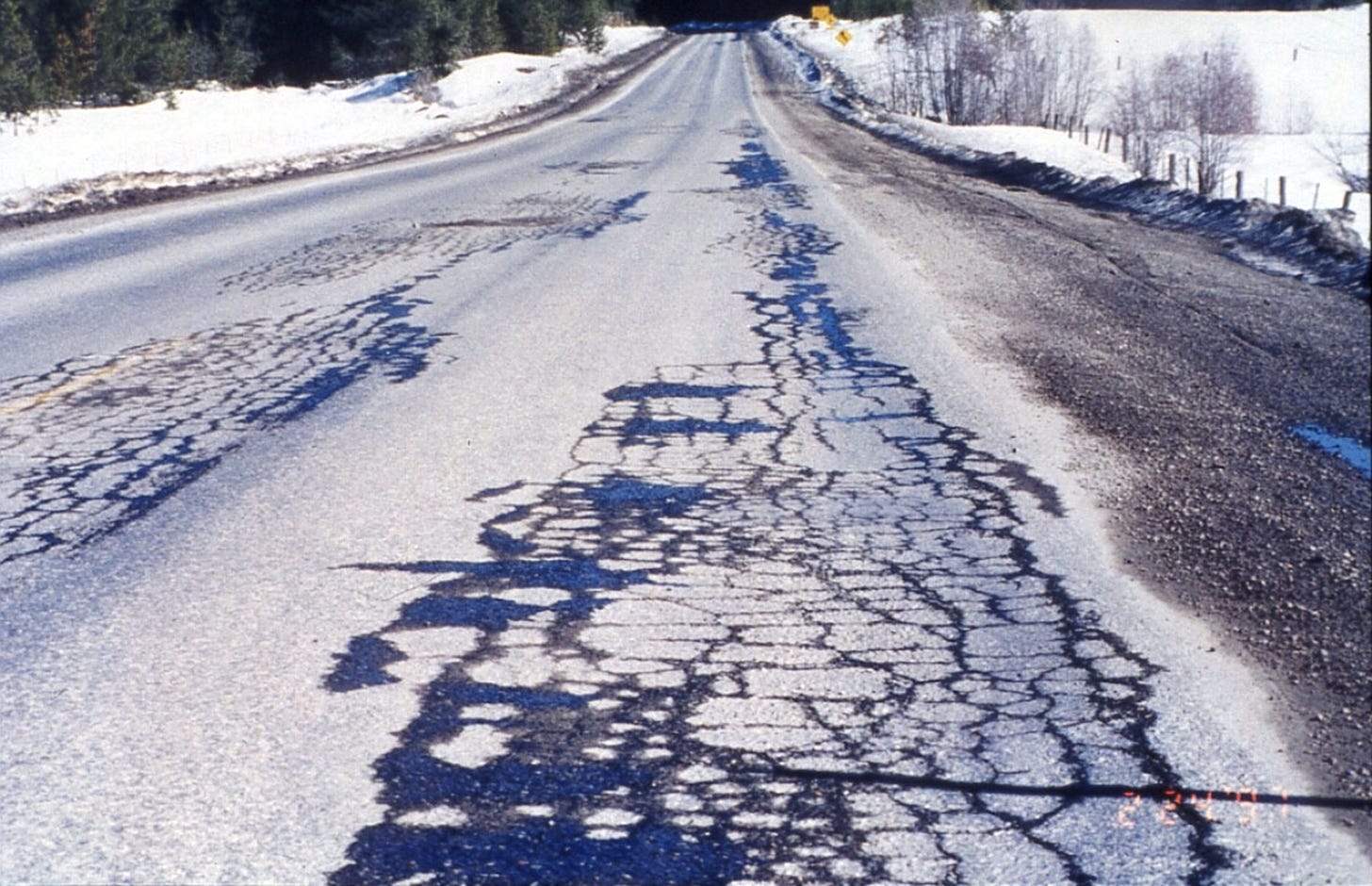
The image vividly depicts the destructive power of frost heave, showcasing a road severely damaged by the upward movement of soil. This visual evidence emphasizes the real-world consequences of this geological phenomenon.
Materials That Help Heating Cables Resist Frost Heave
While no material can completely prevent the powerful forces of frost heave, certain materials used in heating cable construction can significantly mitigate its damaging effects and prolong the cable's lifespan. The key is to create a cable that can flex and withstand some movement without breaking down. Here's how different materials contribute:
Flexible Conductors: The wires that carry the electricity (the conductors) need to be able to bend without snapping. Copper is a common choice, but using stranded copper (many thin wires bundled together) instead of solid copper makes the conductor much more flexible. Think of it like a rope versus a single strand of wire – the rope bends much more easily.
Durable Insulation: The insulating layer surrounding the conductors is crucial. It needs to protect the wires from moisture, chemicals, and, importantly, the stresses of ground movement. Materials like cross-linked polyethylene (XLPE) or silicone rubber are often used because they are more flexible and resistant to cracking than some other plastics. They can handle being bent and stretched a bit without failing.
Tough Outer Jacket: The outermost layer, the jacket, acts as the cable's first line of defence. It needs to be abrasion-resistant (to withstand being dragged through the soil), waterproof, and, crucially, flexible enough to move with the ground. Some jackets are made from specialized polymers that are designed to be both strong and flexible, allowing the cable to "give" a little under pressure from frost heave.
Reinforcement: Some heating cables incorporate reinforcing elements within their structure. This might be a mesh or braid of strong fibers embedded within the jacket or insulation. These reinforcements help to distribute the stress from frost heave across a wider area, reducing the chance of localized damage. Think of it like adding rebar to concrete to make it stronger.
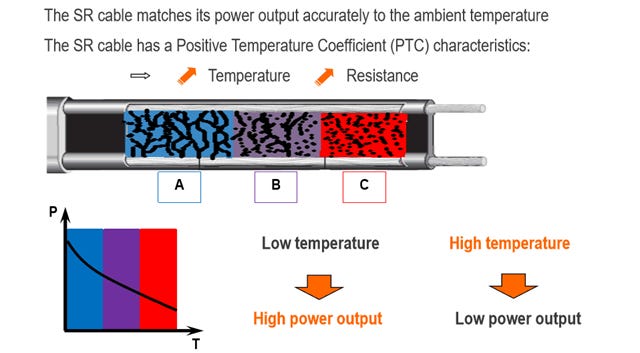
The diagram visually represents the mechanism of heat transfer from the trace heating cable to the surrounding soil. By maintaining a consistent temperature above freezing, the cable effectively prevents the formation of ice lenses and minimizes the impact of frost heave.
Materials That Help Heating Cables Withstand Frost Heave
While no material can completely prevent the powerful forces of frost heave, certain materials used in heating cable construction can significantly reduce its damaging effects and prolong the cable's lifespan. The goal is to create a cable that's flexible enough to withstand some ground movement without breaking. Here's how different materials contribute:
Flexible Conductors (The Wires Inside): The wires that carry the electricity need to bend without snapping. Copper is common, but stranded copper (many thin wires bundled together like a rope) is much more flexible than solid copper (a single thick wire). Think of bending a rope versus a coat hanger – the rope bends much more easily. Stranded copper allows the cable to flex with the ground.
Durable Insulation (The Protective Layer Around the Wires): The insulation protects the wires from moisture, chemicals, and the stresses of ground movement. Materials like cross-linked polyethylene (XLPE) or silicone rubber are often used because they are more flexible and less prone to cracking than some other plastics. They can bend and stretch a bit without failing.
Tough Outer Jacket (The Cable's Outer Shield): The outermost layer protects the cable from abrasion (scratches and cuts), water, and the forces of the soil. It needs to be strong and flexible. Some jackets use specialized polymers (a type of plastic) designed to be both, allowing the cable to "give" a little under pressure from frost heave.
Reinforcement (Extra Strength): Some heating cables have extra reinforcement built in, like a mesh or braid of strong fibres within the jacket or insulation. This helps distribute the stress from frost heave across a wider area, making it less likely to cause damage in one spot. It's like how rebar (steel bars) strengthens concrete.
Table 1: Comparison of Different Sheath Materials
Insulation Material: High-quality insulation is crucial to minimize heat loss and ensure efficient operation of the trace heating system. Common insulation materials include:
Mineral Wool: Providing excellent thermal insulation and resistance to moisture, mineral wool is a widely used insulation material in trace heating cables.
Fiberglass: Offering good thermal insulation properties at a relatively cost-effective price point, fiberglass is another common insulation material used in trace heating cables
The chart visually compares the thermal conductivity of different insulation materials. Lower thermal conductivity values indicate better insulation performance, minimizing heat loss and maximizing energy efficiency.
Real-World Examples of Frost-Resistant Heating Cables
While no heating cable can be completely immune to the powerful forces of frost heave, some are designed with materials and construction techniques that make them much more resistant. Here are a few examples of real-world heating cable products and the features that help them withstand frost heave:
Nelson Heat Trace Cables (Emerson): Nelson makes heating cables specifically for preventing frost heave, often used in large commercial freezers or cold storage. These cables often use:
Cross-linked polyethylene (XLPE) insulation: This type of insulation is flexible and less likely to crack in cold temperatures, which is important when the ground is shifting due to freezing.
Strong and somewhat flexible outer jackets: The outer jacket protects the cable from damage and needs to be able to move a little with the ground. These jackets are often made from special types of plastic polymers.
Stranded copper conductors: The wires inside the cable that carry the electricity are made of many thin copper strands bundled together, like a rope. This makes them much more flexible than a single, solid copper wire, so they can bend without breaking.
You can find more information about these cables on the Emerson website (emerson.com) by searching for "Nelson frost heave cables."
TRM Polymeric Freeze Protection Heating Cables: TRM makes heating cables that are already connected with a plug (pre-terminated) for various uses, including preventing frost heave. Their cables frequently feature:
Insulation and jackets made from special plastic polymers: These materials provide both flexibility and durability when the cables are buried in the ground.
Constant wattage design: This ensures the cable puts out the same amount of heat even if it bends or moves a little, which can happen with frost heave.
You can learn more on the TRM website (trmheatingcables.com) by looking for their product information.
Proper installation and diligent maintenance are crucial for ensuring the effectiveness and longevity of the trace heating system.
Best Practices for Installing Trace Heating Cables:
Installation Depth: The depth of burial varies depending on the application and soil conditions. Proper depth is crucial to ensure effective heat transfer to the soil and prevent damage to the cables.
Cable Spacing: The spacing between cables is determined by the required heat output and the soil properties. Adequate spacing ensures uniform heat distribution and prevents hot spots.
Insulation and Thermal Protection: Adequate insulation and thermal protection are essential to minimize heat loss and ensure efficient operation. Proper insulation helps to maintain the desired soil temperature and reduces energy consumption.
Maintaining Trace Heating Systems for Long-Term Reliability:
Regular Inspections: Regular visual inspections and thermal imaging surveys can help identify potential issues early on, such as cable damage, loose connections, or inadequate insulation.
Routine Maintenance: Periodic maintenance checks, such as cleaning connections and tightening loose fittings, can help prevent problems and ensure optimal performance.
Troubleshooting: Promptly addressing any issues, such as cable failures or insulation damage, can prevent further problems and minimize downtime.
Environmental Impact and Energy Efficiency
Environmental Impact:
Energy Consumption: Trace heating systems consume electricity, which can have an impact on the environment depending on the source of electricity generation. Utilizing renewable energy sources, such as solar or wind power, can significantly reduce the environmental impact of trace heating systems.
Material Selection: Choosing environmentally friendly materials, such as recycled or recyclable materials for the cable components, can minimize the environmental footprint of the system.
End-of-Life Management: Proper disposal and recycling of the cables and components at the end of their service life are essential for minimizing environmental impact.
Energy Efficiency:
Self-Regulating Cables: Utilizing self-regulating cables can significantly improve energy efficiency by adjusting their heat output based on ambient temperature, minimizing energy consumption when it is not required.
Proper Insulation: Adequate insulation minimizes heat loss, ensuring that the generated heat is effectively utilized to prevent frost heave and reducing energy consumption.
Regular Maintenance: Regular maintenance can help identify and address any issues that may be impacting the energy efficiency of the system, such as loose connections or damaged insulation.
Case Studies
Case Study 1: Road Heating in Alaska
Project: A section of the Alaska Highway was experiencing severe frost heave, leading to frequent road closures and costly repairs.
Solution: Trace heating cables were installed beneath the pavement to maintain a consistent soil temperature above freezing.
Results:
Significant reduction in frost heave occurrences.
Reduced maintenance costs due to fewer road repairs.
Improved road safety and reduced traffic disruptions.
Energy Consumption: Data on energy consumption per unit area can be included, along with information on the efficiency of the system and the impact of utilizing renewable energy sources.
Maintenance Costs: Data on maintenance costs over a period of several years can be included, demonstrating the long-term cost-effectiveness of the system.
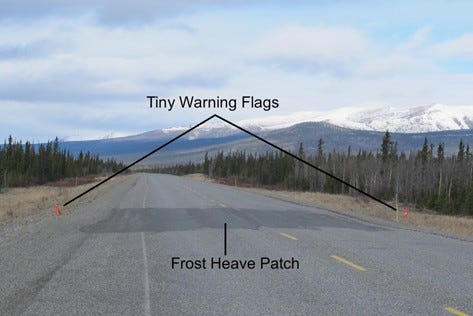
Case Study 2: Pipeline Protection in Canada
Project: An oil pipeline crossing a permafrost region experienced frequent ruptures due to frost heave.
Solution: Trace heating cables were installed along the pipeline to prevent soil freezing and maintain pipeline integrity.
Results:
Elimination of pipeline ruptures caused by frost heave.
Improved safety and reduced environmental risks associated with oil spills.
Energy Consumption: Data on energy consumption for the pipeline section can be included, along with information on energy efficiency measures implemented.
Maintenance Costs: Data on maintenance costs over a period of several years can be included, demonstrating the long-term cost-effectiveness of the system.
Life-Cycle Assessment
A comprehensive life-cycle assessment (LCA) of trace heating systems considers the environmental impacts associated with each stage of their lifecycle:
Material Extraction:
· Environmental impacts associated with the extraction of raw materials for cable manufacturing, such as copper, aluminum, and plastics.
· Consider the environmental impact of mining, transportation, and processing of these raw materials.
Manufacturing:
Environmental impacts associated with the manufacturing process, including energy consumption, emissions, and waste generation.
Assess the environmental impact of manufacturing different cable components, such as the sheath, conductor, and insulation.
Transportation:
Environmental impacts associated with the transportation of raw materials, finished products, and installation equipment.
Consider the impact of transportation distances and modes of transport (e.g., trucks, trains, ships).
Installation:
Environmental impacts associated with the installation process, such as soil disturbance, energy consumption, and waste generation.
Consider the impact of construction equipment and the use of construction materials.
Operation:
· Environmental impacts associated with energy consumption during the operational phase.
· Consider the source of electricity and the associated greenhouse gas emissions.
· Assess the impact of potential leaks or spills of insulating materials.
End-of-Life Disposal:
Environmental impacts associated with the disposal of end-of-life cables and components.
Evaluate the potential for recycling and reuse of materials.
Assess the impact of improper disposal on the environment.
Economic Analysis
A detailed economic analysis of trace heating systems should consider the following factors:
Initial Investment Costs:
Costs associated with the purchase of cables, installation materials, and control systems.
Costs associated with site preparation, installation labor, and project management.
Operating Costs:
Energy consumption costs over the lifetime of the system.
Maintenance and repair costs.
Benefits:
Reduced maintenance costs for infrastructure due to the prevention of frost heave damage.
Improved safety and reduced risk of accidents.
Increased operational efficiency and reduced downtime.
Potential for increased property values and improved infrastructure resilience.
Cost-Benefit Analysis:
Compare the total costs of the trace heating system over its lifetime with the benefits gained.
Conduct a cost-benefit analysis to determine the economic viability of the system.
Compare the cost-effectiveness of different trace heating systems and installation methods.
Recommendations for Using Heating Cables in Cold Climates
Living in a region where temperatures plummet can be a real challenge, especially when it comes to preventing frozen pipes, icy walkways, and snow-covered driveways. Heating cables offer a practical solution to these cold-weather woes, but it's important to consider a few things to ensure they work effectively and safely:
Targeted Use: Heating cables are best used for specific problem areas. Instead of trying to heat your entire yard, focus on key areas like:
Water pipes: Wrap cables around pipes that are prone to freezing, especially those located in unheated spaces like crawl spaces or exterior walls.
Driveways and walkways: Install cables beneath the surface to melt snow and ice, making these areas safer.
Roof edges and gutters: Prevent ice dams from forming by running cables along roof edges and inside gutters.
Choosing the Right Cable: There are different types of heating cables, so selecting the right one for the job is essential:
Self-regulating cables: These cables adjust their heat output based on the surrounding temperature. They're a good choice for preventing frozen pipes because they use more energy when it's very cold and less when it's milder.
Constant wattage cables: These cables produce a consistent amount of heat. They're often used for melting snow and ice on driveways and walkways.
Conclusion
Trace heating cables offer a reliable and effective solution for mitigating the detrimental effects of frost heave in cold regions. By carefully considering the specific application requirements, environmental conditions, and material factors, engineers and contractors can select the most suitable trace heating system to protect infrastructure from the damaging effects of frost heave.
Investing in high-quality trace heating systems provides long-term benefits, including reduced maintenance costs, improved safety, and increased operational efficiency. By embracing this technology and incorporating considerations for environmental impact, energy efficiency, and sustainable practices, communities can mitigate the risks associated with frost heave and ensure the resilience of critical infrastructure in cold climates.
Citations and References
American Society of Civil Engineers (ASCE). (2023). Frost Heave.
https://webstore.ansi.org/preview-pages/asce/preview_9780784405642.pdf
ASTM International. (2022). Standard Test Methods for Evaluating the Performance of Heat Tracing Systems.
Department of Transportation (DOT). (2024). Guidelines for Frost Protection of Pavements.
International Ground Source Heat Pump Association (IGSHPA). (2023). Frost Protection for Ground Source Heat Pumps
National Research Council of Canada (NRCC). (2021). Frost Action in Soils.