Role of Thermal Insulation Materials in Heating Cables: A Comparative Study of Fiberglass and Mineral Wool as an Internal or External Insulation
Ever wondered how the right insulation could make your heating cables work smarter, not harder?
Abstract
In electrical heat tracing systems, the choice of thermal insulation materials plays a pivotal role in enhancing efficiency and performance. This article explores the importance of thermal insulation in heating cables, focusing on the internal and external part of cable, materials that help retain heat and protect the system from environmental elements. By materials like fiberglass, mineral wool, we highlight how each contributes to minimizing energy loss, preventing damage, and optimizing heating performance. The study provides insights into the unique advantages of thermal insulation materials, guiding readers to understand how proper insulation can lead to smarter, more effective heating solutions.
Introduction
Insulation materials in heating cables are typically applied in two primary areas: internally, to protect the conductive core and prevent heat dissipation, and externally, to shield the cable from environmental factors and mechanical stress. Understanding the properties of different thermal insulation materials and their applications is essential for selecting the right material to optimize the heating cable's performance.
Key factors such as thermal conductivity(k), temperature resistance, and mechanical properties are explored to identify the most suitable materials for industrial and residential applications.
Thermal Insulation Materials
In electrical heat tracing systems, especially cables, thermal insulation works by minimizing heat loss and ensuring efficient energy use. The principle of thermal insulation in heating cables involves reducing heat transfer through conduction, convection, and radiation.
Conduction is controlled by using materials with low thermal conductivity, which prevents the heat from escaping along the cable. Convection is reduced by the insulation filling any gaps or cavities, limiting air movement and reducing heat dissipation. Finally, radiation is managed by using reflective materials that direct heat back into the system. By effectively retaining heat within the cable, thermal insulation helps improve the energy efficiency and performance of electrical heat tracing systems.
While there are indeed several thermal insulation materials that exhibit good thermal properties, not all of them are suitable for high-temperature environments like those encountered in electrical heat tracing systems. Materials like polystyrene, polyurethane foam, and cellulose are great for lower-temperature applications, but they struggle in high-heat environments due to limitations in their temperature resistance, fire resistance, and mechanical durability.
However, when it comes to high-temperature environments, mineral wool and fiberglass are excellent choices. These materials have been specifically engineered to withstand high temperatures, offering both thermal insulation and fire resistance.
Composition of Thermal Insulation Materials
Fiberglass is a type of insulation material made from fine fibers of glass. The process involves melting sand, soda lime, and borax into a liquid form, which is then spun into thin fibers. These fibers are woven into a mat or blanket, depending on the application. Fiberglass can also be combined with resins to form rigid boards or batts. Fiberglass is composed primarily of silica (sand), with added boron and alumina to improve its thermal stability, fire resistance, and mechanical properties.
Mineral wool is made from basalt rock, slag, and sometimes limestone, offering superior resistance to high temperatures and better soundproofing characteristics
Key Phenomenon Involved in Thermal Insulation Materials
1. Thermal Conduction and Heat Retention
Fiberglass insulation works by reducing thermal conduction. The glass fibers in the material are designed to resist the flow of heat, keeping the heat generated by the heating element contained within the cable. This minimizes heat loss to the surrounding environment and maintains the desired temperature for the heating system.
The phenomenon of thermal conduction dictates how heat moves through materials. In fiberglass, the low thermal conductivity (typically 0.035 - 0.045 W/m·K) ensures that heat is not lost quickly, making the heating system more efficient.
2. Fire Resistance
Fiberglass insulation is naturally fire-resistant due to its non-combustible nature. This is critical in electrical heat tracing systems because the high temperatures generated by the heating element can lead to fire risks if the insulation is not adequately resistant to flames.
The fire resistance of fiberglass helps prevent the spread of flames and keeps the internal components of the heating cable protected from fire hazards. If the external environment or surrounding materials get exposed to high heat, fiberglass insulation prevents fire damage to the internal wires and heating element.Mineral wool is non-combustible, making it highly effective in preventing fires. In heating cables, high temperatures are generated, and the insulation must prevent the cable from becoming a fire hazard. Mineral wool helps in fireproofing the heating cable by creating a fire-resistant barrier that prevents flames from spreading to the cable's core components.
3. Moisture Resistance
Fiberglass is highly resistant to moisture, which helps protect the inside of the heating cable from water damage. Moisture can lead to corrosion or short circuits in electrical components, and by using fiberglass as insulation, moisture intrusion is significantly reduced. This ensures that the cable maintains its electrical safety and thermal performance even in wet or humid environments.
Mineral wool has high moisture resistance. Mineral wool does not absorb moisture and can function effectively in environments where water or humidity is present. This is essential in electrical heat tracing systems because moisture can cause corrosion, short-circuiting, or reduced insulation performance.
Fiberglass insulation provides an extra layer of mechanical protection to the heating cable. It helps prevent abrasion, scratches, and physical damage that may occur during installation or from external mechanical forces. This is particularly important in industrial settings where cables may be exposed to physical stresses, vibrations, or impacts.
4. Superior Thermal Resistance
Mineral wool has excellent thermal resistance, making it ideal for high-temperature environments. It can withstand extreme temperatures, typically up to 1,000°C, which makes it suitable for industrial applications where heating cables may be exposed to very high operating temperatures. By surrounding the heating element with mineral wool, the heat generated by the cable is efficiently retained within the system, reducing heat loss to the environment.
The thermal resistance of mineral wool helps maintain the consistent temperature of the heating cable, ensuring that it operates at optimal efficiency. This also minimizes the need for additional heating power to compensate for heat loss.
5. Compression Resistance and Durability
Mineral wool is resistant to compression and can withstand physical stresses without losing its insulating properties. Over time, many insulation materials can settle or compress, which reduces their effectiveness. However, mineral wool maintains its shape and effectiveness over the long term, ensuring that the heating cable remains protected throughout its operational life.
Properties
The low thermal conductivity of both fiberglass and mineral wool is due to their fibrous structure, which traps air within the material, reducing heat transfer. This trapped air acts as a thermal barrier, enhancing their ability to resist heat flow. Additionally, the porous nature of both materials further contributes to their low conductivity, making them highly efficient for insulation purposes in high-temperature environments.
Thermal Conductivity (k) is the measure of a material's ability to conduct heat. Lower values are preferred for insulation purposes.
Thermal Resistivity (R) is calculated as the thickness of the material divided by its thermal conductivity. It is a measure of how well a material resists heat flow, where a higher value indicates better thermal insulation properties.
Comparison of Internal and External Insulation
1) Internal Insulation
Fiberglass insulation is commonly used as internal insulation in heating cables due to its excellent thermal stability, high temperature resistance, and mechanical strength. It surrounds the heating element, providing electrical insulation and thermal protection to ensure the efficient functioning of the cable. For temperature exposures greater than 400°F the cable shall have a fiberglass composite between the conductor and jacket.
In Power limiting heating cables, fiberglass plays two key roles:
Carrier for the PTC Conductor: The Positive Temperature Coefficient (PTC) conductor is spirally wrapped around a fiberglass carrier strand, forming a coiled resistor heating element. This coiled heating element is responsible for controlling the temperature and providing the heating function of the cable.
Insulation Between Heating Element and Dielectric Jacket: A fiberglass composite is placed between the heating element and the primary dielectric jacket. This helps to provide additional thermal insulation and mechanical strength.
Mineral wool is not typically used as internal insulation in heating cables. The main reason is that mineral wool is primarily designed for thermal insulation in high-temperature environments, but it does not possess the necessary electrical insulating properties required for the internal insulation of heating cables.
2) External Insulation
External Insulation refers to the insulation material that covers the pipe or tank rather than the overjacket on heating cable.
The overjacket of the heating cable is typically a protective layer that surrounds the cable and shields it from environmental damage, while external insulation refers to materials that are applied to the pipeline or tank in order to reduce heat loss and maintain the required temperature in the system. This external insulation helps to retain the heat generated by the heating cable and protects the system from temperature fluctuations, moisture, and mechanical damage.
Fiberglass is not typically used as an external insulation material for heating cables. On the other hand, for high-temperature applications, mineral wool insulation materials such as Calcium silicate are used externally in power limiting heating cables. These materials offer excellent heat resistance and are often used in power-limiting or mineral-insulated heating systems that operate at higher temperatures .Mineral wool is commonly used as an external insulation in certain electrical heating cables, particularly in high-temperature environments. It offers excellent thermal insulation and is typically applied in applications requiring high heat resistance, such as in mineral-insulated cables (MI cables).
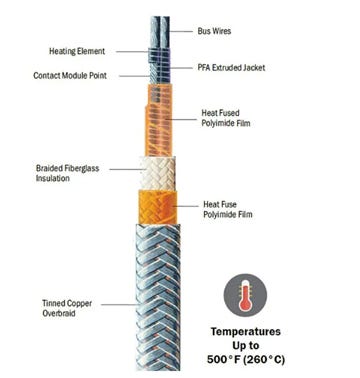
Conclusion
Both fiberglass and mineral wool are highly effective thermal insulation materials widely used in electrical heat tracing systems. Each material has distinct properties that make it suitable for different applications based on environmental conditions and performance requirements. In conclusion, while fiberglass is commonly used as internal insulation in heat tracing systems due to its flexibility, thermal stability, and chemical resistance, mineral wool is primarily used in high-temperature industrial applications and is more suited for external insulation or in mineral-insulated cables (MI cables).For extreme temperature environments where maximum heat resistance is required, mineral wool (often in the form of magnesium oxide) is the preferred option. However, for moderate temperature applications, fiberglass remains a reliable and economical choice.