Self-Healing Materials for Long-Life Heat Tracing Systems
Heat tracing systems are crucial for maintaining process temperatures, preventing pipe freezing, and ensuring efficient industrial operations in various sectors, including oil and gas, chemical processing, and food production. However, traditional heat tracing systems often face durability challenges, especially in harsh environments. Enter self-healing materials—a ground-breaking innovation designed to extend the lifespan of heat tracing systems while reducing maintenance costs and improving overall reliability.
Abstract
Self-healing materials represent a transformative advancement in the durability and efficiency of heat tracing systems, which are vital across industries such as oil and gas, chemical processing, and food production. These materials autonomously repair damage, addressing common challenges like mechanical wear, thermal cycling, and corrosion, thereby extending system lifespan and reducing maintenance costs. This article explores the mechanisms, types, and benefits of self-healing materials, emphasizing their role in enhancing safety, sustainability, and performance. With applications ranging from pipelines to chemical plants, the integration of self-healing technologies signifies a paradigm shift in industrial practices, offering promising future trends such as nanotechnology and smart systems. Investing in these innovations ensures long-term operational efficiency and environmental responsibility.
What Are Self-Healing Materials?
Self-healing materials are advanced composites or coatings engineered to repair damage autonomously without human intervention. These materials mimic biological systems, such as human skin, which can regenerate and repair itself after an injury. By embedding microcapsules, dynamic bonds, or vascular networks into the material, self-healing technology activates when damage occurs, effectively restoring the material’s integrity. An example of a self-healing material is polymer-based coatings with embedded microcapsules containing healing agents. In electrical heat tracing (EHT) systems, such materials can be used in protective cable jackets or insulation coatings, enhancing durability by automatically repairing minor cracks or abrasions that could lead to system failure over time.
Self-Healing Materials: Enhancing the Reliability of Electrical Heat Tracing Systems
Self-healing materials offer a transformative approach to improving the reliability and longevity of electrical heat tracing systems. These innovative materials possess the inherent ability to automatically repair damage, reducing maintenance costs and downtime. The self-healing principle, inspired by biological repair mechanisms, generally involves a multi-stage process tailored for the demands of heat tracing applications:
Damage Detection: In the context of heat tracing, damage might include cracks in the protective jacketing, degradation of insulation, or even minor breaks in the heating element itself. The self-healing mechanism is triggered by this damage. For instance, changes in temperature or electrical conductivity could signal damage.
Healing Agent Release/Activation: Once damage is detected, the healing process is initiated. This could involve the release of a conductive or insulating healing agent to the site of the damage. For example, microcapsules embedded within the jacketing could rupture and release a polymer to seal a crack, protecting the underlying insulation and heating element. In other cases, the damage itself might trigger a chemical reaction in the material, activating the healing process.
Repair Process: The released or activated healing agent then undertakes the repair. For conductive materials used in the heating element, this might involve bridging a small break to restore electrical conductivity. For jacketing or insulation, the healing agent might fill cracks, seal breaches, and restore the protective barrier against moisture and other environmental factors that could compromise the heat tracing system's performance.
Restoration: The final stage sees the damaged area restored. While perfect restoration isn't always achievable, the goal is to regain functionality and prevent further degradation. This could mean restoring the thermal insulation properties of the jacketing, ensuring continued electrical conductivity in the heating element, or both.
Several self-healing mechanisms are being explored for heat tracing applications:
Microcapsules: As mentioned above, these can contain polymers, conductive materials, or other substances tailored to repair specific components of the heat tracing system.
Vascular Networks: A network of channels within the material can contain healing agents that flow to the damaged area, particularly useful for larger-scale damage or in components like the jacketing.
Chemical Reactions: Damage can trigger a chemical reaction that generates a healing agent or causes the material itself to self-repair, especially relevant for materials used in the heating element or conductive pathways.
The Role of Self-Healing Materials in Heat Tracing Systems
Challenges in Traditional Heat Tracing Systems
Heat tracing systems face various challenges, including:
Mechanical Damage: Wear and tear from physical impacts or environmental factors.
Thermal Cycling: Frequent temperature fluctuations can lead to material fatigue.
Corrosion: Exposure to moisture, chemicals, or other corrosive agents.
Maintenance Costs: Regular inspections and repairs increase operational expenses.
How Self-Healing Materials Solve These Issues
Extending Lifespan: Repairing microcracks and preventing them from propagating.
Reducing Downtime: Minimizing the need for manual repairs.
Improving Safety: Maintaining system integrity even in extreme conditions.
Enhancing Sustainability: Lowering material waste and energy consumption associated with repairs.
Types of Self-Healing Materials for Heat Tracing Systems
Polymer-Based Materials
Polymers are widely used in heat tracing systems due to their flexibility and thermal insulation properties. Incorporating self-healing polymers ensures that cracks or abrasions are repaired automatically, maintaining the insulation's effectiveness over time.
Coatings with Microcapsules
These coatings contain microcapsules filled with healing agents. When the coating is damaged, the capsules rupture, releasing the healing agent to seal the crack and restore functionality.
Metal-Based Self-Healing Alloys
Metallic materials with self-healing capabilities are ideal for high-temperature applications. These alloys can repair microcracks through diffusion processes or by utilizing embedded healing agents that react under heat.
Among these materials, the specific self-healing materials used in heat tracing systems are:
Coatings with Microcapsules – These coatings are applied to heating cable jackets or protective outer layers. When the coating is scratched or damaged, embedded microcapsules rupture, releasing a polymeric healing agent that seals the breach, preventing moisture ingress and maintaining insulation integrity.
Self-Healing Polymers – These materials are primarily used in insulation layers and protective sheathing of electrical heat tracing cables. They can autonomously repair minor cracks through dynamic bonding or embedded microcapsules, preventing degradation and prolonging system lifespan.
While metal-based self-healing alloys have self-repairing capabilities, their use in electrical heat tracing is less common compared to polymer-based coatings and insulation
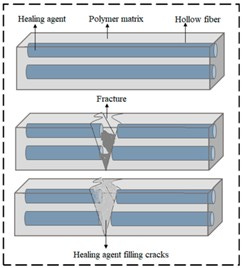
Benefits of Self-Healing Heat Tracing Systems
Enhanced Durability: With the ability to self-repair, these systems withstand harsh environmental conditions longer than traditional materials.
Cost Efficiency: Reduced maintenance needs lead to significant cost savings.
Improved Performance: Continuous functionality ensures optimal heat transfer and system reliability.
Environmental Impact: Fewer replacements and repairs contribute to sustainability.
Applications of Self-Healing Heat Tracing Systems
Self-healing materials have broad applications across industries:
Oil and Gas
Pipelines in the oil and gas sector often operate in extreme temperatures and corrosive environments. Self-healing heat tracing systems ensure consistent performance, reducing the risk of pipeline failures and costly downtime.
Chemical Processing
Chemical plants require precise temperature control to maintain product quality. Self-healing materials enhance the reliability of heat tracing systems, ensuring uninterrupted operations.
Food and Beverage Industry
Heat tracing systems are critical for preventing frozen pipes and maintaining hygiene standards. Self-healing materials provide long-lasting solutions, minimizing disruptions in production processes.
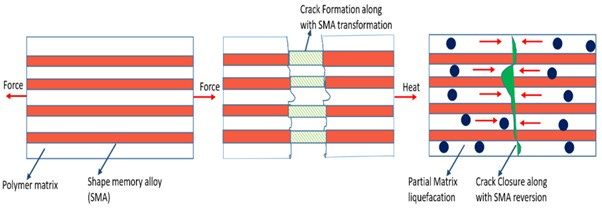
Left Panel: Shows the undamaged state of the material, with SMAs integrated into the polymer matrix.
Middle Panel: Under mechanical force, cracks form in the polymer, causing deformation.
Right Panel: When heat is applied, the SMA undergoes reversion, closing the cracks. The polymer partially liquefies, filling the gaps, and the material's integrity is restored.
Implementing Self-Healing Heat Tracing Systems
Selecting the Right Materials
Choosing the appropriate self-healing material depends on factors such as:
Operating temperature range
Environmental conditions (e.g., moisture, chemicals, UV exposure)
System design and application requirements
Installation Best Practices
To maximize the benefits of self-healing materials:
Assess Compatibility: Ensure the material is compatible with existing system components.
Follow Manufacturer Guidelines: Adhere to installation procedures to achieve optimal performance.
Regular Monitoring: While self-healing materials reduce maintenance needs, periodic inspections ensure early detection of potential issues.
Future Trends in Self-Healing Materials for Heat Tracing Systems
The field of self-healing materials is rapidly evolving, and several promising trends are emerging. These trends aim to enhance the capabilities of self-healing materials, making them more efficient, responsive, and environmentally friendly. Here's how the three trends you mentioned relate to self-healing materials:
Nanotechnology Integration: Nanotechnology involves the use of nanoparticles to improve the properties of materials. In the context of self-healing materials, nanoparticles can be incorporated into the material's structure to enhance its self-healing capabilities. For example, nanoparticles can act as carriers for healing agents, facilitating their release and promoting faster and more efficient healing. They can also strengthen the material's matrix, making it more resistant to damage and improving its overall durability.
Smart Systems: The integration of self-healing materials with smart systems, such as IoT sensors, enables real-time monitoring and diagnostics. Sensors can detect damage in the material and trigger the self-healing process automatically. This combination allows for proactive maintenance and prevents minor damage from escalating into major failures. Smart systems can also provide valuable data on the material's condition, helping to optimize its performance and extend its lifespan.
Green Materials: The development of bio-based self-healing composites aligns with the growing emphasis on sustainability. Green materials are derived from renewable resources and have a lower environmental impact compared to traditional materials. By incorporating bio-based components into self-healing materials, we can create more eco-friendly solutions for various applications, including heat tracing systems
Frequently Asked Questions (FAQs)
How do self-healing materials work?
Self-healing materials repair damage through mechanisms such as microcapsule rupture, dynamic chemical bonding, or diffusion processes, depending on the material type.
Are self-healing heat tracing systems expensive?
While initial costs may be higher, the long-term savings from reduced maintenance and extended lifespan make them cost-effective.
Can self-healing materials withstand extreme temperatures?
Yes, advanced self-healing materials are designed to function effectively in high-temperature environments, making them suitable for industrial heat tracing applications.
Conclusion
Self-healing materials are revolutionizing the durability and efficiency of heat tracing systems. By addressing common challenges such as mechanical damage, thermal cycling, and corrosion, these materials ensure long-lasting performance in demanding industrial settings. Investing in self-healing heat tracing systems not only reduces maintenance costs but also enhances safety and sustainability
References
White, S. R., et al. "Autonomic healing of polymer composites." Nature, 409, 794-797, 2001
Toohey, K. S., et al. "Self-healing materials with microvascular networks." Nature Materials, 6, 581-585, 2007
Brown, E. N., et al. "Repeated healing of a self-healing polymer." Advanced Materials, 14(23), 1850-1853, 2002.
Williams, H. R., and Trask, R. S. "Self-healing composite materials for aerospace applications." Proceedings of the Institution of Mechanical Engineers, Part G: Journal of Aerospace Engineering, 221(4), 553-558, 2007