Understanding Polymer Aging in Electrical Heat Tracing Systems: A Focus on XLPE and EPR/EPDM
— Environmental Factors, Causes of Degradation, Real-World Applications in Nuclear Power Plants, and Prevention Strategies for Prolonging Cable Life —
Abstract
Electrical Heat Tracing Systems play a critical role in maintaining the temperature of pipelines and equipment across industries such as oil, gas and nuclear power. However, the long-term reliability of these systems is compromised by the aging of the polymer insulation materials used in heating cables. This article explores the environmental factors contributing to polymer degradation, particularly focusing on Cross-Linked Polyethylene (XLPE) and Ethylene Propylene Rubber (EPR/EPDM) in nuclear power plants. It also discusses the underlying causes of polymer degradation and highlights nondestructive monitoring methods, particularly on capacitive sensing that can detect early signs of aging. Real-life applications, such as the use of these polymers in nuclear power plants, are examined, along with solutions for mitigating aging and prolonging cable life.
Introduction to Polymer Aging and Degradation
Polymer aging in EHT cables is the process of gradual degradation in the insulation and outer jacket due to environmental stressors like heat, moisture, UV exposure, and chemical contact. These factors erode the mechanical and electrical properties of the polymer over time, compromising the overall performance and reliability of the cables. Cross-Linked Polyethylene (XLPE) and Ethylene Propylene Rubber (EPR/EPDM) are among the most commonly used polymers in EHT cables due to their excellent thermal stability and dielectric properties. However, despite their robustness, these polymers are not immune to aging, which can lead to mechanical deterioration, insulation failures, and potential system breakdowns. This article delves into the key environmental factors driving polymer aging, the underlying degradation mechanisms, and provides strategies to mitigate these effects. It also highlights real-world cases and explores the role of nondestructive monitoring techniques in maintaining the reliability of EHT systems.
Environmental Factors leading to Polymer Aging in EHT Cables
Polymer insulation in Electrical Heat Tracing cables is subjected to a range of environmental factors that accelerate aging and degradation. These factors weaken the polymers' mechanical and electrical properties, eventually leading to insulation failures and system malfunctions. Key environmental stressors include heat, moisture, UV radiation, and chemical exposure, all of which play a significant role in the aging process.
1. Heat Exposure:
EHT cables operate in high-temperature environments, and prolonged heat exposure can cause thermal degradation of polymer insulation. In materials like XLPE, which has a melting point of 110-125°C, high temperatures can break down the crystalline structure, leading to reduced dielectric properties and embrittlement. EPR/EPDM polymers, with a melting point of 120-130°C, are more resistant to high temperatures but still experience oxidative degradation, resulting in reduced flexibility and eventual cracking.
2. Moisture Ingress:
Moisture can infiltrate polymer insulation over time, especially in environments with high humidity or direct exposure to water. This leads to swelling, decreased dielectric strength, and possible electrical breakdown. XLPE and EPR are hydrophobic, but long-term moisture exposure, especially in submerged or humid environments, can cause degradation.
3. UV Radiation:
Outdoor EHT systems are often exposed to ultraviolet (UV) radiation, which degrades the surface of polymers like XLPE over time, causing discoloration, embrittlement, and surface cracking.
4. Chemical Exposure:
In industrial environments, cables may encounter chemicals such as solvents, oils, and corrosive substances. EPR/EPDM, though chemically resistant, can degrade when exposed to harsh solvents, while XLPE may undergo oxidation when exposed to chemicals at elevated temperatures.
Why Focus on XLPE and EPR/EPDM Polymer Aging in EHT Cables?
Cross-linked Polyethylene (XLPE) and Ethylene Propylene Rubber/Ethylene Propylene Diene Monomer (EPR/EPDM) are the predominant insulation materials used in EHT systems, especially in critical applications like nuclear power plants. According to the 1994 Electric Power Research Institute (EPRI) report, 89% of U.S. nuclear power plants use XLPE for low-voltage cable insulation, while 73% use EPR/EPDM. These polymers are widely favored for their excellent thermal stability, flexibility, and dielectric properties, making them well-suited for EHT cables that must withstand high temperatures, electrical stress, and harsh environmental conditions. However, despite their excellent properties, XLPE and EPR/EPDM are still susceptible to aging and degradation due to long-term exposure to harsh environments eventually leading to cracking and insulation breakdown
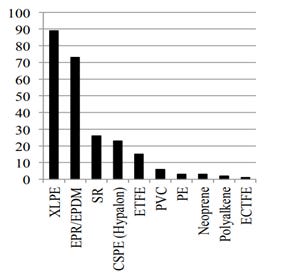
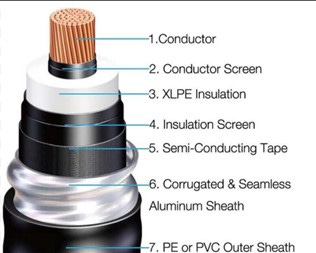
Key Characteristics of XLPE and EPR/EPDM
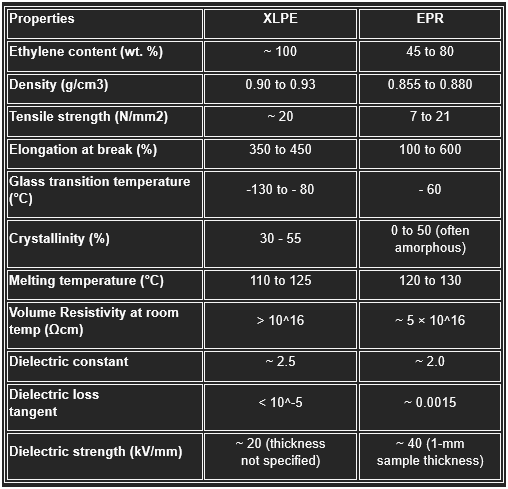
Comparison of XLPE and EPR insulation based on their properties
When comparing Cross-Linked Polyethylene (XLPE) and Ethylene Propylene Rubber (EPR/EPDM) for Electrical Heat Tracing applications, both materials offer distinct advantages based on their unique physical and electrical properties. XLPE has higher mechanical strength with superior tensile strength and a higher crystallinity, making it more rigid and ideal for applications where mechanical robustness and dimensional stability are critical. It also has excellent thermal stability and operates well in cold environments due to its low glass transition temperature, preventing cracks under freezing conditions. However, XLPE has lower flexibility compared to EPR/EPDM.
On the other hand, EPR/EPDM provides greater flexibility with a wider range of elongation at break, making it ideal for applications requiring dynamic movement or installations where the cable must bend frequently. It also has superior dielectric strength, making it suitable for high-voltage applications, and its higher melting temperature allows it to withstand constant high-temperature environments better than XLPE. EPR/EPDM also performs well in humid or chemically exposed environments, as it offers better resistance to moisture ingress and chemical degradation.
Common Causes of Polymer Degradation in EHT Cables
1. Arrhenius and Non-Arrhenius Behaviors
The Arrhenius model or Arrhenius behavior is a formula used to predict the rate of chemical reactions, including degradation processes, based on temperature. It is named after Swedish chemist Svante Arrhenius, who proposed that reaction rates increase exponentially with temperature. The formula is:
Where:
k is the rate constant of the reaction (or degradation rate in the case of polymers),
A is the pre-exponential factor (frequency of collisions leading to reactions),
E_a is the activation energy required for the reaction to occur,
R is the universal gas constant, and
T is the absolute temperature in Kelvin.
In this model, the degradation rate of polymers, such as those used in EHT cables, increases exponentially with higher temperatures. For example, a small increase in operating temperature could lead to a significant acceleration of polymer degradation, causing a faster breakdown of insulation materials. The Arrhenius model helps engineers estimate the remaining useful life (RUL) of materials based on temperature stress and adjust system operation accordingly.
However, while the Arrhenius model works well for simple chemical reactions, it doesn't always accurately predict the degradation behavior of complex polymers like XLPE AND EPR/EPDM, particularly at different temperature ranges or in real-world applications. Many polymers exhibit non-Arrhenius behavior, where degradation rates do not follow a simple exponential relationship across all temperatures, especially around phase transitions like melting points.
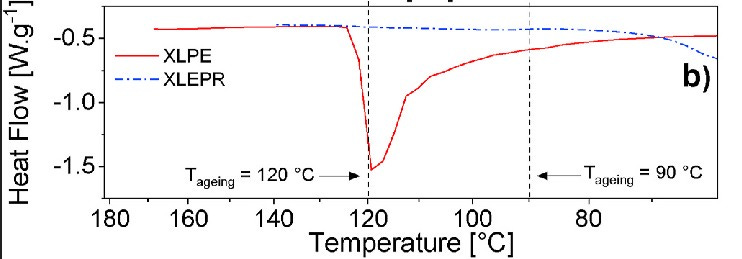
2.Gas Evolution
During the radiation-induced degradation of polymers, gases such as hydrogen and methane are evolved. The production of these gases can lead to internal pressure, causing mechanical strain and potentially leading to cracks. The presence of oxygen during aging results in additional gas evolution, including water vapor and carbon dioxide, which can exacerbate the degradation process.
3. Cross-Linking and Chain Scission
As polymers degrade, molecular changes such as cross-linking and chain scission occur. Cross-linking refers to the formation of new bonds between polymer chains, while chain scission involves the breaking of polymer chains. In the presence of oxygen, chain scission is more dominant, leading to the formation of free radicals that accelerate degradation. Cross-linking typically occurs in oxygen-free environments, changing the material's properties.
4. Oxidation and Antioxidant Depletion
Oxidation is a major cause of polymer degradation. Antioxidants are added to polymers like XLPE and EPR/EPDM to prevent oxidation by interacting with peroxy radicals and hydro-peroxides. However, over time, antioxidants are depleted, and once they fall below a critical threshold, the material’s mechanical properties begin to degrade rapidly. Depleted antioxidants result in faster aging, leading to embrittlement and cracking.
5. Inhomogeneous Oxidation
In real-world environments, oxidation does not occur uniformly. Inhomogeneous oxidation occurs when oxygen diffusion is slower than the rate of degradation, leading to uneven degradation across the material. This can cause localized cracks in heating cables, which eventually propagate and cause failure.
Preventing Polymer Aging in EHT Systems
Preventing or slowing down polymer aging in EHT systems involves several strategies:
Proper Installation:
Ensuring that cables are installed in controlled environments where they are protected from moisture, direct sunlight, and high temperatures can reduce the rate of aging. Installing protective conduits or UV-resistant coatings can further help reducing polymer aging.
Regular Monitoring:
Nondestructive methods like capacitive sensing allow for continuous monitoring of cable insulation, enabling early detection of degradation and timely maintenance or replacement.
Temperature Management:
Maintaining operating temperatures within the recommended range for the polymer can prevent accelerated thermal aging.
Capacitive Sensing for Monitoring Polymer Aging in EHT Cables
To detect early signs of polymer aging, nondestructive monitoring methods are used. Capacitive sensing is a key nondestructive method used to monitor insulation degradation in Electrical Heat Tracing cables, specifically focusing on insulation materials like XLPE and EPR. In the case of XLPE-insulated heating cables, capacitive sensing can detect early signs of cracking, brittleness, or other forms of mechanical deterioration caused by prolonged exposure to high temperatures and oxidative processes. For EPR/EPDM-insulated cables, the method is highly effective in identifying moisture ingress, which can compromise the electrical performance of the insulation.
By continuously monitoring the dielectric characteristics, capacitive sensing provides real-time data on the health of the polymer, allowing for timely maintenance and replacement before insulation failure occurs. This is particularly valuable in nuclear power plants, where downtime for cable inspection is impractical, and system integrity is critical.
Real-Time Monitoring of Heating Cables in Harsh Environments
One of the significant advantages of capacitive sensing is its ability to perform in situ, real-time monitoring of cable aging in challenging environments, such as nuclear power plants or extreme industrial settings. Traditional mechanical tests to assess insulation integrity would require cable disassembly or system shutdown, which is often impractical in such environments. Capacitive sensing, however, allows continuous monitoring without physical interference, ensuring that degradation trends are identified early. This capability is particularly useful for EHT cables exposed to high temperatures, chemicals, or moisture, where insulation integrity is critical to maintaining system reliability and safety.
Conclusion:
Safeguarding EHT Systems Against Polymer Aging
Polymer aging is a critical factor in the reliability of Electrical Heat Tracing systems, particularly for materials like XLPE and EPR/EPDM. Environmental factors such as heat, moisture, UV radiation, and chemical exposure significantly contribute to the degradation of these polymers. Understanding the causes of degradation and implementing preventive strategies can extend the life of EHT cables and reduce the risk of system failures. Nondestructive monitoring methods like capacitive sensing provide a valuable tool for early detection of insulation degradation, enabling proactive maintenance and improved safety in industries like nuclear power.
Citations and References:
Aging Mechanisms and Monitoring of Cable Polymers:
Degradation of polymeric power cable due to water treeing under AC and DC stress:
Aging Mechanisms and Non-Destructive Aging Indicators of XLPE/CSPE Unshielded LV Nuclear Power Cables Subjected to Simultaneous Radiation-Mechanical Aging: