Understanding Thermal Cycling Stress: Enhancing Durability of Self-Regulating Heating Cables
In an industry where reliability and efficiency are paramount, can we afford to overlook the longevity of self-regulating heating cables?
Abstract
This article explores the challenges of thermal cycling stress on self-regulating heating cables, focusing on how repeated heating and cooling cycles lead to material fatigue and compromise durability. Thermal cycling stress varies significantly with temperature: at low temperatures, brittleness can cause microcracking, while high temperatures lead to expansion, softening, and potential oxidation. Practical solutions to counter these effects include selecting durable insulation materials(including comparison table of various materials), deploying heat-tracing controllers to manage temperature fluctuations, integrating design adaptations like expansion loops, and scheduling regular maintenance. By applying these strategies, industries can significantly enhance the lifespan, reliability, and cost-effectiveness of their heating cable systems, reducing the risk of failures and downtime in high-demand applications.
Problem
Industries that rely on self-regulating heating cables face a significant challenge with thermal cycling stress arising from repeated heating and cooling cycles. These fluctuations cause materials in the cables to expand and contract, leading to mechanical fatigue, microcracking, and, over time, a reduction in the cables' structural integrity.
Purpose
The purpose of our article is to shed light on the specific challenges posed by thermal cycling stress and offer practical solutions for mitigating its effects. By educating industry professionals on the causes and consequences of this stress, as well as providing actionable strategies such as material selection, thermal insulation, and proactive maintenance, the article aims to help industries extend the lifespan and maximizing durability of their heating cable systems.
Thermal Cycling Stress: How It Differs at Low and High Temperatures
Introduction
Thermal cycling stress refers to the mechanical stress generated in materials due to repeated temperature fluctuations. As temperatures change, materials expand and contract. Over time, these cyclical movements lead to mechanical fatigue, deformation, or even failure. While this phenomenon is especially critical for equipment like pipelines and traditional electrical cables, self-regulating heating cables (SR cables) are specifically designed to adapt to temperature variations, mitigating the direct impact of thermal cycling stress. However, other environmental factors, such as prolonged exposure to extreme temperatures, can still influence the durability and performance of SR cables.
Science behind thermal cycling stress
The amount of expansion or contraction depends on the material’s thermal expansion coefficient. Thermal cycling becomes problematic when materials undergo frequent heating and cooling over time. Each cycle adds mechanical stress, which eventually leads to fatigue and cracking.
Formula:
where
σ: Thermal stress (Pa)
E: Young’s modulus of the material (Pa)
α: Coefficient of thermal expansion (1/°C)
ΔT: Temperature difference between cycles (°C)
Below is a graph showing how thermal stress accumulates over time during thermal cycling at different temperature ranges.
Thermal cycling stress at low temperature
At low temperatures, materials often exhibit brittleness, losing their elasticity and becoming more susceptible to fracture under stress, which increases the likelihood of sudden failures in various applications. Additionally, the reduced thermal expansion at low temperatures results in less pronounced changes in size and shape, as the temperature fluctuations per cycle tend to be smaller, posing challenges in accommodating thermal stresses, particularly in systems designed for higher operational temperatures. This brittle behavior facilitates the formation of microcracks during thermal cycling, leading to accelerated fatigue and a significant reduction in structural integrity. Moreover, some materials may exhibit delayed recovery, meaning they do not return to their original shape immediately after contraction, which can lead to cumulative stress within the material. Understanding these behaviors is essential for selecting appropriate materials and designing systems that can withstand the challenges posed by low-temperature environments.
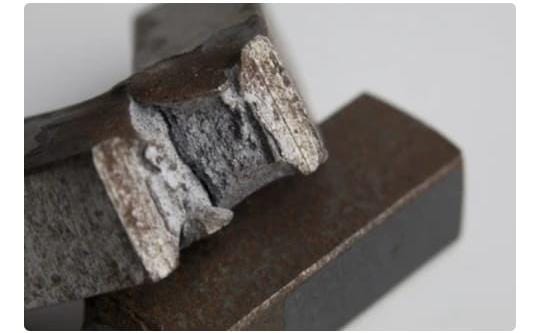
Thermal cycling stress at high temperature
At elevated temperatures, materials experience softening, which increases their ductility, allowing them to stretch without breaking. This characteristic is critical in applications where materials must accommodate thermal expansion. As the temperature rises, materials undergo higher expansion, leading to more significant internal stress if they are restrained. This phenomenon can result in mechanical failures if not properly managed.
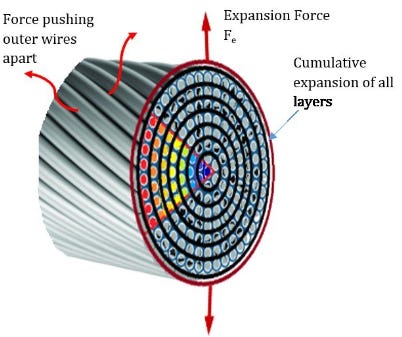
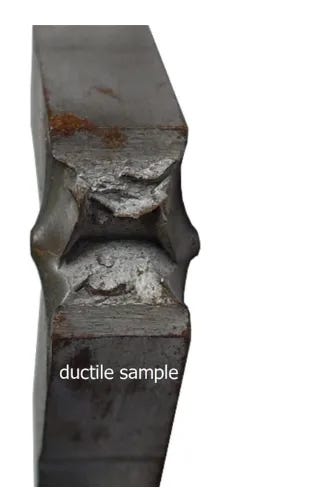
Furthermore, prolonged exposure to high temperatures leads to the creep effect, a gradual deformation that occurs over time. This slow deformation amplifies stress buildup during thermal cycling, contributing to the material's fatigue. Additionally, exposure to elevated temperatures can cause oxidation and degradation in metals and polymers, which may induce chemical changes that weaken their structural integrity. As a result, the likelihood of failure increases, emphasizing the need for careful material selection and engineering design in high-temperature applications.
Comparison
Challenges Faced by Industries Due to Thermal Cycling Stress
Industries that use self-regulating heating cables often face several challenges when it comes to managing thermal cycling stress:
Material Fatigue and Cracking: The most common issue is material fatigue, where repeated thermal cycling leads to the formation of cracks in the insulation or the conductive core of the cable. These cracks can worsen over time, leading to failure of the heating system.
Reduced Cable Flexibility: In environments where cables experience low temperatures, brittleness sets in, reducing the flexibility of the cables and increasing the likelihood of mechanical failure.
Chemical Degradation at High Temperatures: When exposed to high temperatures for extended periods, materials such as the cable’s outer jacket can degrade, reducing the overall durability of the system.
Increased Maintenance Costs: The frequent need to inspect and replace damaged sections of cables due to thermal cycling increases operational and maintenance costs for industries.
Risk of System Downtime: Unaddressed thermal cycling stress can lead to unexpected failures, causing system downtime, which can result in significant financial losses, especially in critical processes like oil refineries or chemical plants.
Decrease in Heat Output: As thermal cycling stress progresses, one of the primary challenges observed in self-regulating heating cables is a gradual decrease in output efficiency. Repeated expansion and contraction can degrade the cable's conductive pathways over time, leading to reduced heat output. Eventually, if left unaddressed, this decline may reach a point where the cable can no longer function effectively as a heater.
Mitigation Strategies for Thermal Cycling Stress
While thermal cycling stress poses challenges, there are effective strategies industries can adopt to mitigate its effects and extend the life of self-regulating heating cables.
Select High-Quality Materials
Advanced Insulation Materials: Utilize insulation materials with high thermal stability and resistance to cracking. For instance, fluoropolymers like PTFE and FEP offer excellent thermal and chemical resistance, while silicone rubber provides flexibility and resilience to thermal cycling.
Fluoropolymers Comparison Table:
PTFE versus PFA
PTFE has a slightly higher heat resistance, the melting points of PFA and PTFE are 260°C and 327°C respectively.
Water absorption (permeability) and weathering affect PFA more than PTFE, although PFA is superior in resistance to salts.
Like PTFE, PFA has excellent resistance to cracking and stress and a low coefficient of friction.
The electrical insulating capacity (dielectric strength) of PTFE is excellent, but PFA is still 3-4 times higher. For gas and liquid systems this will not be decisive very often.
The main difference is that PFA can be molten and PTFE cannot. PFA can be formed by conventional injection moulding or screw extrusion. PTFE on the other hand can only be machined by turning and milling. That gives other possibilities for the shapes to be made. You could call PFA the injection mould version of PTFE
PFA is often preferred when high reliability is required in environments with high chemical, thermal and mechanical stresses. In summary, PFA combines high thermal stability, chemical resistance, and flexibility, which are essential for reducing thermal cycling stress and maximizing the lifespan of self-regulating cables.
Silicon Rubber: Silicone rubber has good heat resistance in high-temperature environments and can maintain its elasticity and mechanical properties within the range of − 50 to 250 °C.
Conductive Core Materials: Opt for cores made from high-quality conductive polymers that maintain performance over a wide temperature range. Various conductive polymers and their properties are shown below:
Employ Heat Tracing Controllers:
Controllers, such as Proportional Ambient Sensing Controllers (PASC), optimize power use based on ambient conditions, reducing unnecessary heating and extending cable life. They adjust heat output dynamically and help avoid overheating, which can otherwise accelerate material fatigue in SR cables. PASC uses an electronic controller to sense ambient temperature and continuously adjust the controller’s duty cycle to provide the heat tracing power needed for a piped system.
Employ Heat Tracing Controllers:
Controllers, such as Proportional Ambient Sensing Controllers (PASC), optimize power use based on ambient conditions, reducing unnecessary heating and extending cable life. They adjust heat output dynamically and help avoid overheating, which can otherwise accelerate material fatigue in SR cables. PASC uses an electronic controller to sense ambient temperature and continuously adjust the controller’s duty cycle to provide the heat tracing power needed for a piped system.
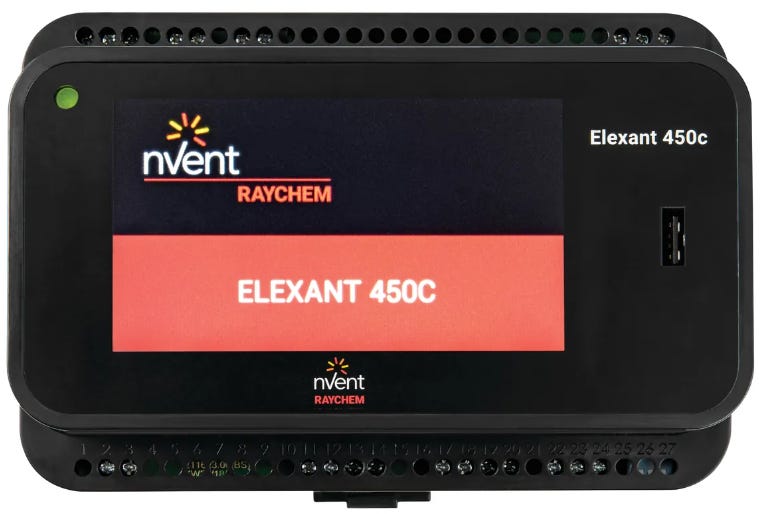
Flexible temperature control of pipe freeze protection and grease line maintenance systems.
Line sensing and/or ambient sensing.
Proportional Ambient Sensing Control (PASC) algorithm for enhanced energy savings in ambient sensing mode.
Alarm relay with change over contact to signal power, temperature or communication problems.
Design Adaptations for Thermal Cycling:
Avoid Air Pockets: Ensure the cable is installed without air gaps to prevent overheating and ensure efficient heat transfer. Air pockets can lead to hot spots and potential cable damage.
Allow for Thermal Expansion: Incorporate loops or bends in the cable layout to accommodate thermal expansion and contraction, reducing mechanical stress on the cable.
Use Appropriate Accessories: Employ compatible power connection kits, end termination kits, and splice kits to maintain the integrity of the cable system and protect against moisture ingress.
Controlled Expansion: Incorporating expansion joints into the design of piping and heating systems allows for controlled movement of materials as they expand and contract. These joints help absorb the mechanical stress caused by thermal cycling, preventing the stress from being transferred to the heating cables themselves. link
Regular Maintenance and Inspection:
Proactive scheduled maintenance is essential for detecting early signs of thermal fatigue. Regular inspections allow for the identification of cracks, brittleness, or any other signs of wear before they become significant issues. Replacing damaged sections of cables or applying protective coatings can prevent system-wide failures.
Conclusion
Thermal cycling stress is an unavoidable challenge in many industrial applications, but with proper understanding and mitigation strategies, its effects can be managed. By carefully selecting materials, implementing insulation and expansion solutions, and maintaining proactive monitoring and maintenance schedules, industries can significantly extend the lifespan of their self-regulating heating cables. Addressing the challenges posed by thermal cycling stress not only improves the reliability of heating systems but also reduces maintenance costs and minimizes the risk of system downtime, ultimately enhancing overall operational efficiency.